History & Development Of the Key Role Masking Tape For Auto Body
Automotive Masking Tape History
Automotive masking tape is a specially designed type of tape that has revolutionized the automotive industry, enabling precise and efficient painting processes. Its origins can be traced back to the early 20th century when the automotive industry was rapidly expanding, and the need for masking surfaces during painting arose.
In the 1920s, masking tapes made from paper or cloth with adhesive coatings were first introduced, allowing painters to protect areas they didn’t want to paint. However, these early tapes often left residue or failed to withstand the high temperatures and harsh chemicals used in automotive painting processes.
It wasn’t until the 1950s and 1960s that advancements in adhesive and backing materials led to the development of specialized automotive masking tapes. These tapes were designed to resist high temperatures, solvents, and chemicals, while also providing clean removal without leaving residue on the vehicle’s surface.
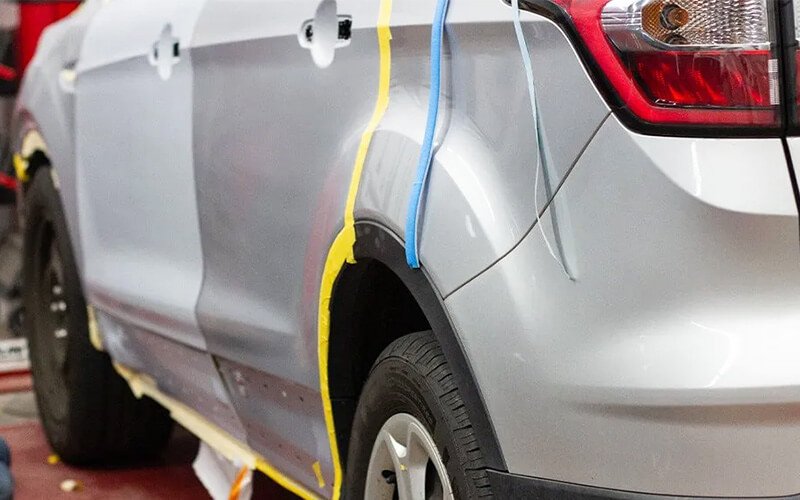
Introduction to Automotive Masking Tape
The introduction of automotive masking tapes revolutionized the painting process, enabling higher quality finishes and reducing the time and labor required for surface preparation and cleanup. This innovation played a crucial role in the growth and efficiency of the automotive industry, allowing for faster production cycles and more consistent paint jobs.
Today, automotive masking tapes are an indispensable tool in the industry, used in various applications beyond just painting, such as:
- Protecting surfaces during welding, sanding, or rust removal processes.
- Masking off areas for precise application of sealants, adhesives, or sound-damping materials.
- Bundling and organizing wires, cables, and hoses during assembly or repairs.
- Creating crisp, clean lines and patterns for custom paint jobs or vehicle wraps.
The impact of automotive masking tapes on the industry cannot be overstated. They have contributed to:
- Improved efficiency and productivity in manufacturing and repair processes.
- Higher quality finishes and consistent results in automotive painting.
- Reduced material waste and environmental impact through precise masking.
- Facilitated the growth of custom automotive painting and detailing services.
- Enabled new techniques and applications in vehicle restoration and modification.
As the automotive industry continues to evolve, masking tapes will undoubtedly play a pivotal role in enabling new technologies, production methods, and design innovations, further pushing the boundaries of what is possible in automotive manufacturing and customization. For more other Automotive industries tapes, you could check the details from previous post-How Industrial Tapes Revolutionized the Automotive Manufacturing Industry.
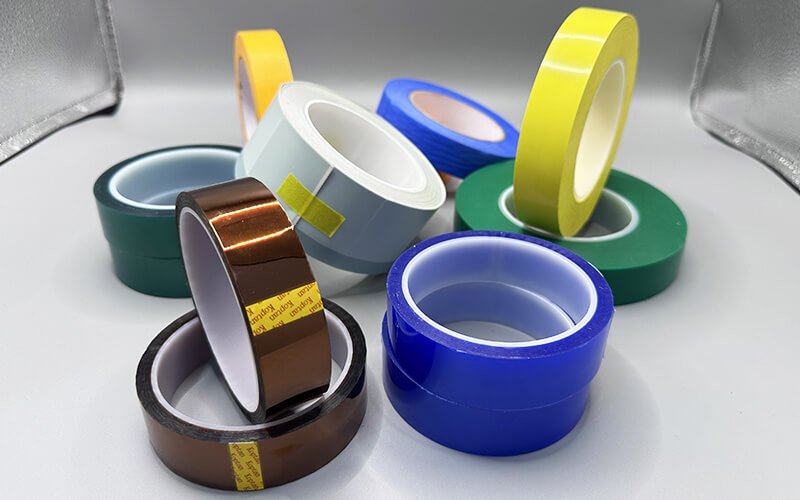
As automotive masking tapes evolved, they developed several crucial features that make them well-suited for various applications in the automotive industry. These features include:
Heat Resistance: Modern automotive masking tapes are designed to withstand high temperatures, often up to 300°F (149°C) or higher. This heat resistance is essential for withstanding the intense heat encountered during automotive painting processes, such as in paint booths or baking cycles.
Solvent and Chemical Resistance: Automotive paints, thinners, rust inhibitors, and other chemicals used in the industry can be highly corrosive. High-quality masking tapes are formulated to resist degradation from exposure to these harsh solvents and chemicals, ensuring clean removal without residue or adhesive transfer.
Clean Removability: A key attribute of automotive masking tapes is their ability to remove cleanly from surfaces without leaving behind any adhesive residue or damaging the underlying material. This is crucial for maintaining the integrity of painted surfaces, body panels, and other components.
Conformability: Many automotive masking tapes are designed with a flexible backing material that can conform to curved surfaces, contours, and intricate shapes found on vehicles. This ensures proper masking and prevents paint bleed or overspray in hard-to-reach areas.
To achieve these crucial features, DCA Tape introduce automotive masking tapes are typically made from different backing materials:
1. Paper Masking tape:
Carrier Material: Crepe Paper / Washi Paper
Colors: 12 different colors options
Width and Length: Customized
High Heat (℃): Up to 180℃
2. PVC Masking Tape:
Carrier Material: PVC
Colors: Blue / Green / Yellow
Width and Length: Customized
High Heat (℃): Up to 200℃
3. PET Tape & Polyimide Tape:
Depending on the specific material and construction, auto body masking tapes can be utilized in various areas of a vehicle, including:
Exterior Body Panels: Paper or cloth-based tapes are ideal for masking off body panels, door jambs, and trim during painting or refinishing work.
Glass and Windows: Low-tack, easy-release tapes are well-suited for masking window glass and rubber seals without causing damage or adhesive transfer.
Engine Bay and Underhood: High-temperature cloth tapes are essential for protecting engine components, wiring harnesses, and other underhood areas during painting or repair work.
Interior Surfaces: Precision-edged paper tapes can mask off interior panels, trim pieces, and upholstery for precise application of sealants, sound-damping materials, or touch-up painting.
Wheels and Tires: Specialized high-tack tapes can securely mask off wheels, tires, and brake components during refinishing or customization work.
By carefully selecting the appropriate type of automotive masking tape based on the application, material compatibility, and environmental conditions, automotive professionals can ensure efficient, high-quality results while protecting valuable vehicle components from potential damage or contamination.